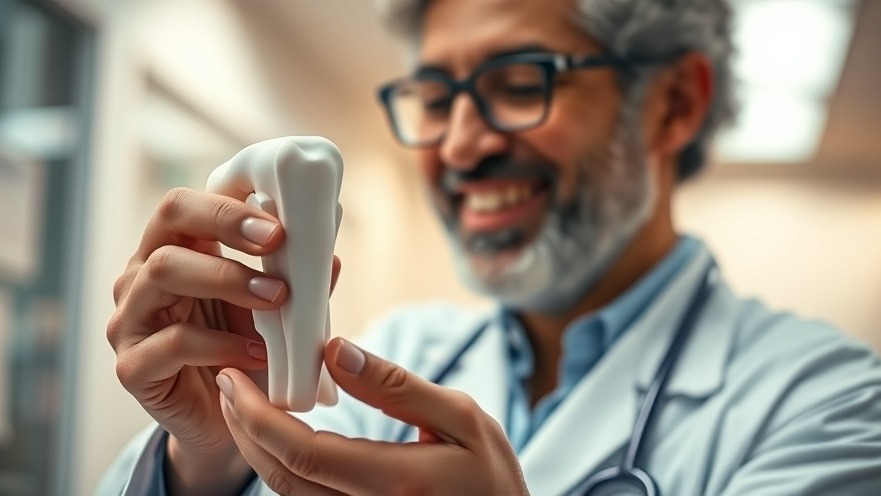
3D-Printed Knee Implants: A Leap Towards Personalized Orthopedic Solutions
The realm of orthopedic surgery is on the brink of a revolutionary leap forward thanks to advances in 3D printing technology. Customized and patient-specific implants, particularly in knee replacement surgeries, are transforming surgical methodologies. With the potential to enhance the reliability and mechanical properties of cobalt-chromium-molybdenum (CoCrMo) alloy knee implants, innovations in laser powder bed fusion (LPBF) technology are paving the way for a future where implants are exactly tailored to fit every patient's unique anatomical structure.
Why Personalized Implants Matter
Amid increasing demand for knee replacement solutions, fueled by an aging population and the rise of active lifestyles among younger individuals, the quest for implants that provide not only functionality but also fit and comfort has never been more critical. Orthopedic R&D teams are focused on understanding the specific biomechanical requirements of each patient. The collaborative research by Naton Biotechnology and notable universities has resulted in a groundbreaking 3D-printed knee implant which recently gained approval from China's National Medical Products Administration.
Personalized implants, which accurately replicate the kinematic profile of individual patients, offer significant advantages over conventional off-the-shelf options. The introduction of advanced designs, supported by rapid and precise 3D printing technologies, means that surgeons can provide better-aligned and biomechanically optimal solutions. Ken Gall, Co-founder of restor3d, affirms that the shift from standard implants to customized solutions is essential for improving patient satisfaction and surgical outcomes.
The Mechanics of 3D Printing in Implants
The development of the new CoCrMo alloy implants was particularly innovative in that it addressed the anisotropic properties that traditional 3D printing methods often face. Anisotropy refers to the directional dependency of material properties, which can lead to inconsistent physical performance in clinical applications. Researchers tackled this issue by optimizing heat treatment processes, improving the mechanical strength and reliability of the implants.
The layer-by-layer manufacturing process of CoCrMo alloy in LPBF requires careful control to prevent common pitfalls such as porosity and residual stress, which can detrimentally impact an implant’s performance. Studies reveal that patient-specific adjustments in design not only mitigate such risks but also enhance the overall efficacy of the implants. This demonstrated capability suggests a future where every knee implant can be designed with unique, individualized support structures that improve both immediate post-operative recovery and long-term joint health.
Pioneering Techniques and Future Trends
The collaborative efforts in developing 3D-printed knee implants have introduced innovative techniques such as the use of negative Poisson's ratio (−υ) materials. Such materials have the ability to expand laterally when stretched, potentially enhancing engagement and integration with surrounding tissue. This is crucial for knee joint functionality since it mimics the natural mechanics of human bone, providing a framework through which healing and integration can be optimized.
As the orthopedic industry pushes towards personalization, methods like the proxy-model developed within the current research play a crucial role. This allows developers to predict and tailor the properties of implants to meet specific mechanical and biological requirements. Future advancements could also include the integration of bioactive coatings and smart materials that promote better integration with natural bone as well as infection resistance, thus addressing a longstanding concern surrounding implant longevity.
Conclusion: An Era of Change in Orthopedic Solutions
The emergence of 3D-printed knee implants signifies a pivotal point in orthopedic surgery, one that embraces personalization, innovation, and enhanced therapeutic outcomes. As organizations invest heavily in research and development, materials like CoCrMo superalloy combined with cutting-edge manufacturing technologies illustrate the potential for creating implants that not only meet but exceed current orthopedic standards. Healthcare practitioners, especially concierge health practitioners, will need to keep pace with these innovations as they reshape medical care delivery and orthopedic solutions. Thus, understanding these trends is not just beneficial; it is essential for optimizing patient care and embracing the future of surgery.
Write A Comment